
RISK, HAZARD, NEAR MISS, ACCIDENT AND INCIDENT
* The terms hazard and risk are often used together, but it is important to have a clear understanding of their distinctions. Let's explore this further:
Imagine you are performing maintenance on a 15KVA electricity transformer in your laboratory. If safety procedures are not followed, there is a potential for accidents and injuries. In this case, the transformer itself is the hazard, as it poses a potential danger. The likelihood of an accident occurring while working on the transformer is known as the risk. However, by implementing proper health and safety measures such as wearing personal protective equipment (PPE) to minimize the impact of a fall and following standard safety protocols like obtaining a safety permit, opening circuit breakers, opening isolators, and closing earth switches, the risk of injury can be effectively mitigated.
Now, let's consider a situation where all the necessary safety precautions have been taken, except for closing the earth switches. This unsafe condition of working on the transformer without closing the earth switches is referred to as a near miss, which should be reported. Similarly, working on the transformer without wearing PPE would also be considered a near miss.
A near miss is an event that does not result in injury, illness, or damage, but has the potential to do so. It often occurs due to a combination of hazardous conditions that, if left unaddressed, could eventually lead to an accident. While near misses are not accidents themselves, they serve as valuable indicators of potential risks. Therefore, it is crucial to report all near misses, regardless of their severity, to ensure appropriate measures are taken to prevent future incidents that could result in serious harm or loss.
In contrast, an accident is an unplanned event that results in personal injury or illness, and may also cause property damage. On the other hand, an incident is an unplanned event that does not result in personal injury or illness, but may lead to property damage.
Unsafe Act - Performance of a task or other activity that is conducted in a manner that may threaten the health and/or safety of workers. For example:
· Lack of or improper use of PPE.
· Failure to tagout/lockout.
· Operating equipment at unsafe condition.
· Failure to warnpeople in the area of work activity.
· Bypass or removal of safety devices.
· Using defective equipment.
· Use of tools for other than their intended purpose.
· Working in hazardous locations without adequate protection or warning.
· Improper repair of equipment.
Unsafe Condition - A condition in the workplace that is likely to cause property damage or injury. For example:
· Defective tools, equipment, or supplies.
· Inadequate supports or guards.
· Inadequate warning systems.
· Fire and explosion hazards.
· Poor housekeeping.
· Uneven walking surfaces.
· Excessive noise.
· Poor ventilation.
WHAT IS CONSIDERED A SAFETY HAZARD?
Any unsafe behavior or condition that could lead to an injury of a person or property damage if the behavior or condition is not corrected.
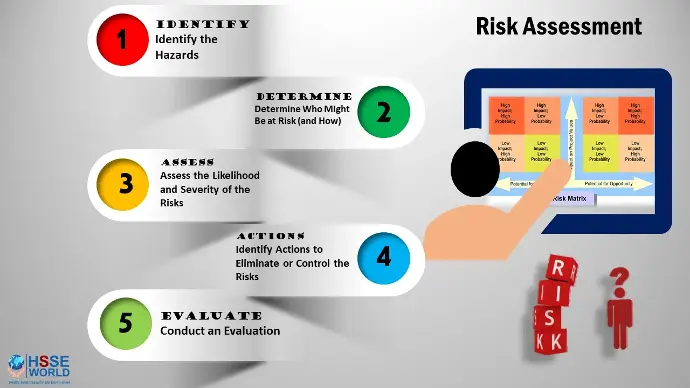
RISK MANAGEMENT STEPS
Risk management should identify potential hazards and determine controls that can be implemented to eliminate or reduce any risks to employees, operations, and/or property. A new risk assessment should be completed and documented each time a new potentially hazardous experiment is carried out. After control measures are implemented, standard operating procedures and training should be followed to ensure employees are aware of the correct steps to take and can reference such material as needed. There are three main steps to complete this include:
Step 1: Identify General Hazards and analyze
Mark off known risks of the hazardous agents, processes and equipment. Use this list as a tool to help complete the risk assessment in step 2.
Step 2: Define Risk Assessment
Fill out the risk assessment form. Please note, EH&S can assist in filling out parts of the risk assessment if the information is not known.
Step 3: Assess the risk assessment
Input the hazardous process, chemical/substance or hazardous equipment “Identify General Hazards”
“Significant Hazard,” input the hazard that relates to the hazardous process, chemical/substance, or equipment. SDS is a useful piece of information for this section
“Initial Risk Level,” use the risk matrix tool to determine if the risk is low, medium or high.
“Control Measures,” input what control measures are in place to reduce the risk.
“Final Risk Level,” should indicate the final risk level, after control measures are in place. Use the Risk Matrix tool. The final risk level should be less than the initial risk level.
Step 4: Action Plan - implement control measures and create standard operating procedures (SOPs) and training.
Step 5: Evaluate Plan - to identify the success of your plan

Here are some links to resources on risk management guidelines in clinical laboratories:
1. Clinical Laboratory Improvement Amendments (CLIA) - https://www.cms.gov/Regulations-and-Guidance/Legislation/CLIA
2. College of American Pathologists (CAP) - https://www.cap.org/
3. American Society for Clinical Laboratory Science (ASCLS) - https://ascls.org/
Please note that specific risk management guidelines may vary depending on the type of laboratory and the tests being performed. It is important for laboratory staff to stay informed about the latest guidelines and regulations to ensure the safety and accuracy of laboratory testing.